In Episode 169 of the Disruptors for Good podcast, I speak with Dr. Jules Hammond, CEO & Co-founder of BeFC, on biofuel cells and the future of sustainable batteries.
Listen to more Causeartist podcasts.
Every year, billions of batteries are thrown out with little thought as to their environmental impact. Traditional batteries often contain toxic materials, metals, and dangerous electrolytes, which can have a devastating effect on the environment.
Fortunately, BeFC biofuel cells offer a revolutionary alternative. Combining advanced chemistry and nanomaterials, these cells are capable of providing high performance energy in a safe and sustainable way.
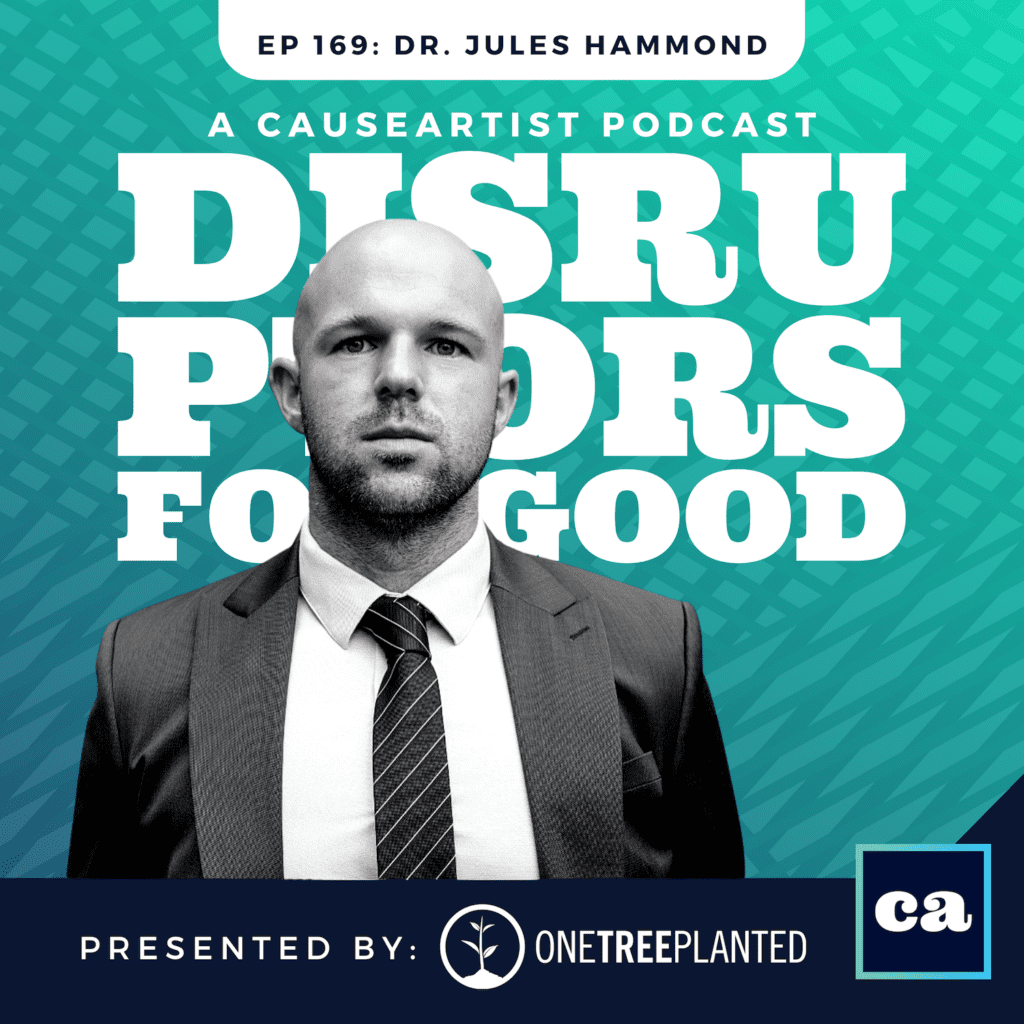
How Do BeFC Biofuel Cells Work?
BeFC biofuel cells rely on organic materials to generate energy. The cells use an electrochemical process that converts chemical energy into electrical energy through oxidation-reduction reactions.
The paper-based biofuel cells are a revolutionary, eco-friendly solution to the complexity and financial burden associated with traditional miniature batteries. Thin, light-weight and flexible yet degradable – they reduce environmental impact while still remaining economically responsible.
This allows them to generate consistent power without needing to be charged or replaced like traditional batteries do.
The BeFC Digital Platform
With the advancement of digital systems, BeFC has developed an innovative union between sensor technology and wireless communication. The custom-made hardware and firmware have been refined to work harmoniously with the fuel cell technology for unbeatable data readout performance.
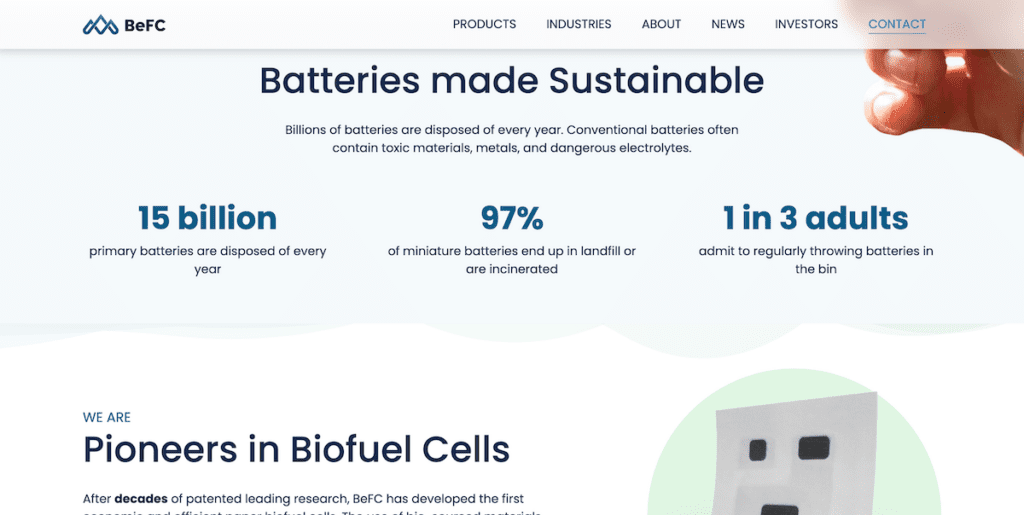
The Paper Biofuel Cell
BeFC offers an eco-friendly energy solution with dynamic adaptability – capable of meeting the unique demands and technical requirements of customers. The form factor allows for seamless integration into your products, providing reliable power solutions.
The Benefits of Using BeFC Biofuel Cells
The benefits of using BeFC biofuel cells are numerous. They provide an eco-friendly alternative to conventional batteries, eliminating the need for toxic chemicals and metals while still offering high performance energy.
As a result, they require less waste than traditional batteries and can save you money in the long run by reducing your reliance on disposable batteries over time.
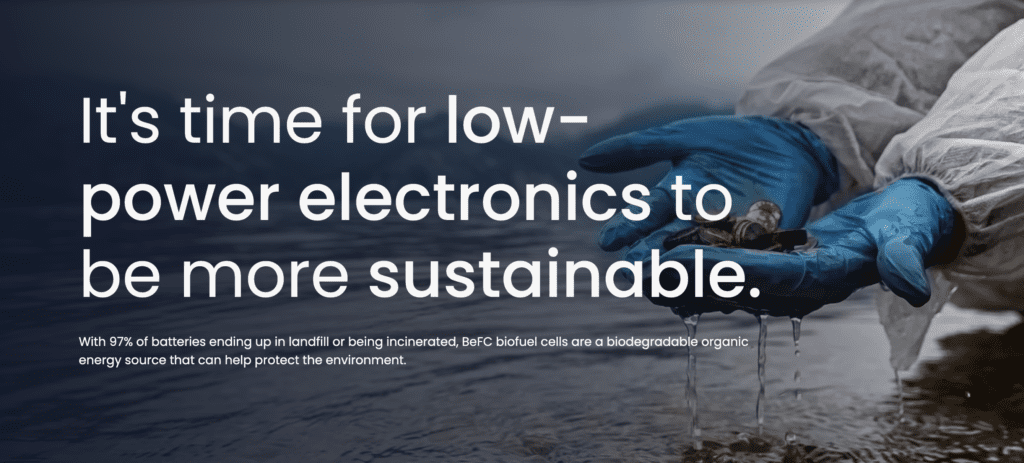
BeFC biofuel cells offer a unique solution for powering everyday electronics such as wearables, logistics, medical, and healthcare in a safe and sustainable way.
By utilizing advanced chemistry and nanomaterials, these cells provide consistent power with no need for charging or replacing like traditional batteries do – making them both environmentally friendly and cost effective in the long run.
With so many benefits to offer, it’s clear why BeFC biofuel cells are revolutionizing the way we power our devices today.
Interview Transcript
00:10
Host: Well, thank you so much, Jules, for joining me today. I’m really excited to talk about everything you and BFC have created and are working on in the battery space. As the world becomes increasingly reliant on batteries, sustainability in this sector is much needed. Before we dive into what BFC is and what it does, could you talk a little about your journey and the light bulb moment that led to the creation of BFC?
00:58
Jules Hammond: Thank you. My personal background is in electronic engineering. I studied a Bachelor’s and Master’s before doing a PhD in bioelectrochemistry. After my PhD, I returned to my birth city of Grenoble in the Alps to join a research group focused on implantable biofuel cells.
The vision was to power devices like pacemakers and insulin pumps using the body’s energy by harvesting glucose and oxygen to create electricity. But when I joined the team, I realized that marketing and selling implantable devices is incredibly complicated and expensive. I wondered if we could use the same technology to power small portable devices. We decided to power a digital pregnancy test, specifically a Clearblue test, by replacing the two alkaline batteries with our paper biofuel cell technology.
Once we demonstrated this, it became clear that there were many opportunities in single-use medical tests and other markets like wearables for sports, luxury packaging, and logistics tracking. That was the birth of BFC, founded in May 2020. We are on a mission to provide low-cost, low-environmental-impact electronic solutions.
02:40
Host: Amazing. You mentioned some of the industries, but how does the technology actually work for something like a wearable compared to an implantable device using glucose and oxygen?
03:05
Jules: Previously, we took glucose from the bloodstream and oxygen dissolved in the blood. Now, on a piece of paper, we use oxygen from the air and glucose stored inside the paper. The device needs to be activated with a drop of liquid. For a wearable sports device, you could use sweat to activate it.
For logistics tracking, we’ve developed a liquid reservoir or blister packaging. When you pop this blister, it releases liquid into the fuel cell, activating the device, and it starts producing electricity.
04:07
Host: How long do these batteries last? Are they for single-use, multiple-use, and how do you know when they need replacing?
04:18
Jules: BFC focuses on short-term use cases, ideally lasting a few days. For longer durations, we have to carefully manage the energy stored in the paper. For example, in logistics tracking, to track for two weeks, you need to manage how many measurements you take and how many wireless messages you send.
We are focused on single-use disposable solutions, such as digital pregnancy tests, ovulation tests, or biomarker tests, and smart wearables that measure data periodically.
05:10
Host: Before BFC, what was the environmental impact of single-use devices like pregnancy tests, and how does BFC’s solution improve this?
05:46
Jules: The current estimate is around 15 billion primary batteries disposed of each year, which is about 78 million batteries per day. Ninety-seven percent of miniature batteries end up in landfills or are incinerated.
Collecting, processing, sorting, and recycling these tiny batteries is complicated and expensive, often resulting in landfill or incineration. BFC aims to replace some of these miniature batteries with our technology, reducing the environmental impact.
06:57
Host: Do BFC batteries need to be recycled, or do they biodegrade over time?
07:08
Jules: It can be both. Some customers prefer recycling, while others focus on biodegradation or composting. We’ve done composting trials and found that in industrial compost, our technology loses more than 50% of its mass after 45 days.
We aim to reduce the environmental impact, and while recycling is great, the small quantity of paper and carbon we use means it has a minor effect. We aim to eliminate the challenges posed by traditional batteries, such as fire risks and toxic hazards.
08:42
Host: What does R&D look like for BFC, from initial idea to product development and customer purchase?
08:59
Jules: BFC is built on decades of pioneering research. We’ve been leaders in implantable fuel cells and enzyme sensing for years. Our co-founder and product manager, Dr. Murray Burch, played a key role in making our technology economically viable by selecting enzymes that can be produced at a large scale.
Now, we’re focused on mass production, transitioning from producing 1,000 units per day to 1 million units per day. This involves moving from traditional materials to a printed process, which is key for addressing this huge problem.
10:27
Host: What industries are the biggest consumers of your product right now? Is it healthcare, wearables, IoT devices, or something else?
10:42
Jules: Logistics is probably our biggest traction point right now, tracking high-value assets like pallets of luxury clothing. The regulatory aspect in logistics is lower than in medical devices.
However, interest from the medical sector is significant, and wearable technologies are growing. Once we start deploying BFC technology in wearable patches, this market could grow substantially.
11:30
Host: Are the batteries the same across different industries, or do you make adjustments based on specific needs?
11:42
Jules: We can adjust the materials, shape, and size of our fuel cells to meet different market sectors and use cases. Depending on the sensors and wireless communication used, we tailor the BFC technology accordingly.
For example, if a product needs to operate in harsh environments, we might change the exterior layer of the BFC to be more robust, water-resistant, or oil-resistant.
12:32
Host: What are some common questions or hesitations from customers before implementing BFC into their supply chain?
12:59
Jules: One common question is about the battery’s lifetime. Some alkaline batteries can last five to ten years, while ours are designed for shorter durations. Another concern is temperature sensitivity.
Our biofuel cells use enzymes that work best at body temperature, but higher temperatures can denature the enzymes. Thermal cycling can also stress the enzymes, leading to reduced functionality. These limitations mean our technology is not suitable for extreme outdoor environments for long periods.
14:42
Host: When you talk about scaling from 1,000 to 1 million units per day, how important is funding in this process? Is there demand at that scale already?
15:07
Jules: Funding is crucial. The processes used at small and large scales are different, requiring new equipment and machinery. There’s also a development phase to perfect the process. Venture capital funding is essential to purchase machinery, develop processes, and scale up production. The venture capital world sees the potential and is willing to take the risk to fund this growth.
16:05
Host: Are the machines custom-made?
16:11
Jules: The machines are standard in one sense, but you need to fit them with specific modules for different functions like cutting, printing, and assembly. Chaining these modules together requires working on interfaces, which takes time and money.
16:43
Host: Is 3D printing an option for this technology?
16:51
Jules: We don’t use much 3D printing. Instead, we use rotary screen printing and flexographic printing, which are much faster. 3D printing is not yet a solution for the throughput we need, which is meters per minute.
17:23
Host: Looking at the future, what are some goals and successes BFC aims to achieve in the next three to five years, or even a decade?
17:58
Jules: Our first goal is to achieve industrial-scale production of 1 million units per day. We also aim to incorporate printed electronics and circuits into our products. Eventually, we want BFC to provide its own products, identifying market interests and offering low-cost, low-environmental-impact solutions directly.
18:48
Host: Thank you so much for taking the time to talk with us. Best of luck to you and the team at BFC in your endeavors. It’s incredible work that will have a significant impact on global sustainability. Thanks for taking the time.
Jules: Thank you. Thank you very much.